Tests
Using different transducers for the sonification, i.e. excitation of the welds.
Aluminium - Aluminium, Copper - Aluminium
Aluminium and copper plates are welded together using various transducers operating at frequencies of 20 kHz, 28 kHz, and 40 kHz in a contactless mode. Additionally, welding is conducted without sonification as a reference.
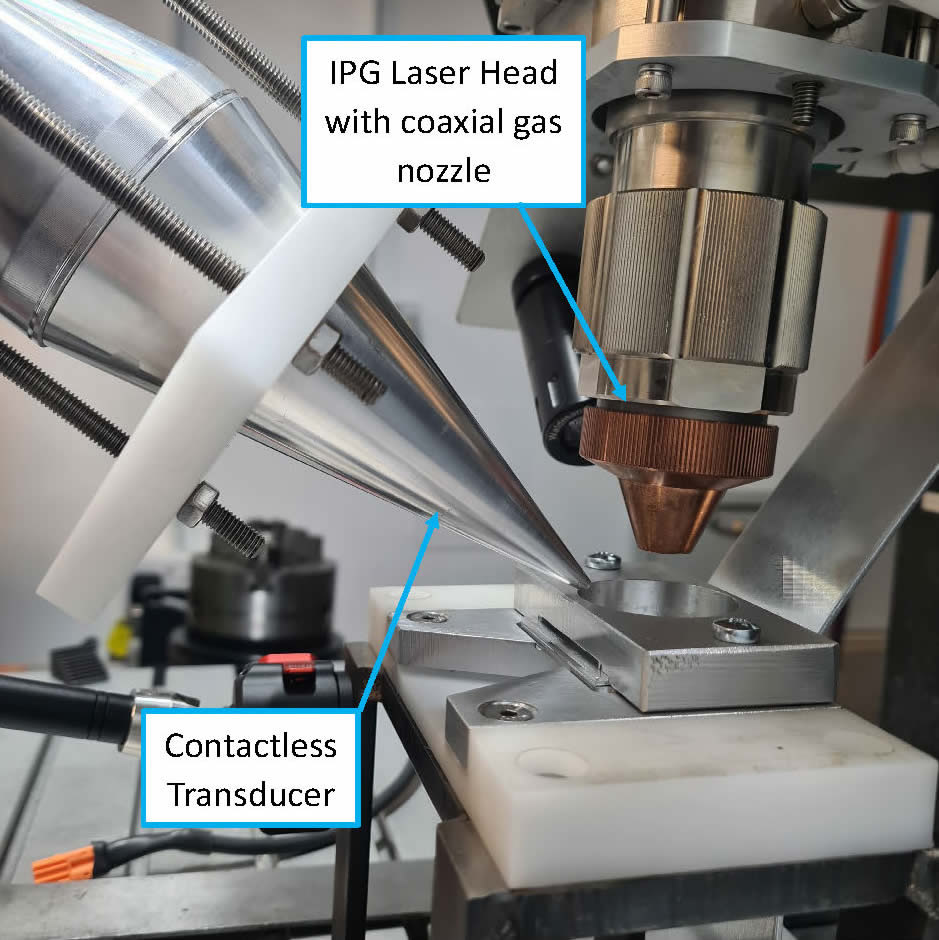
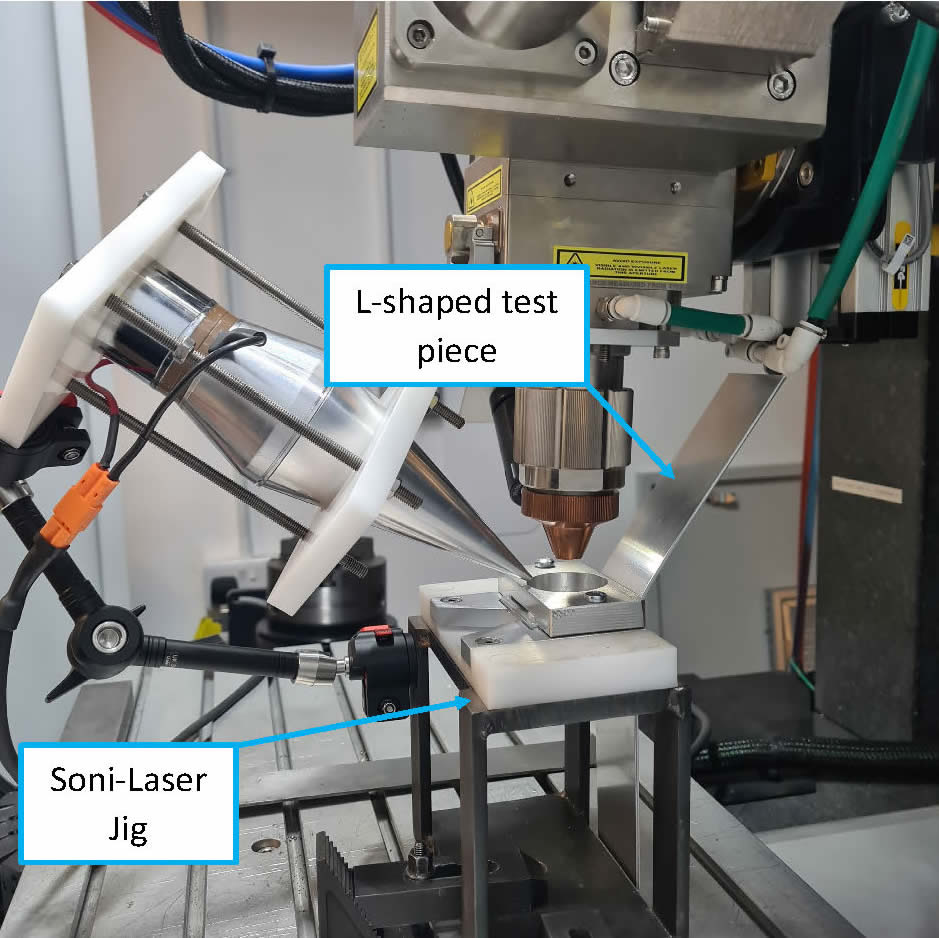
Pressure vibration in the diffusing field
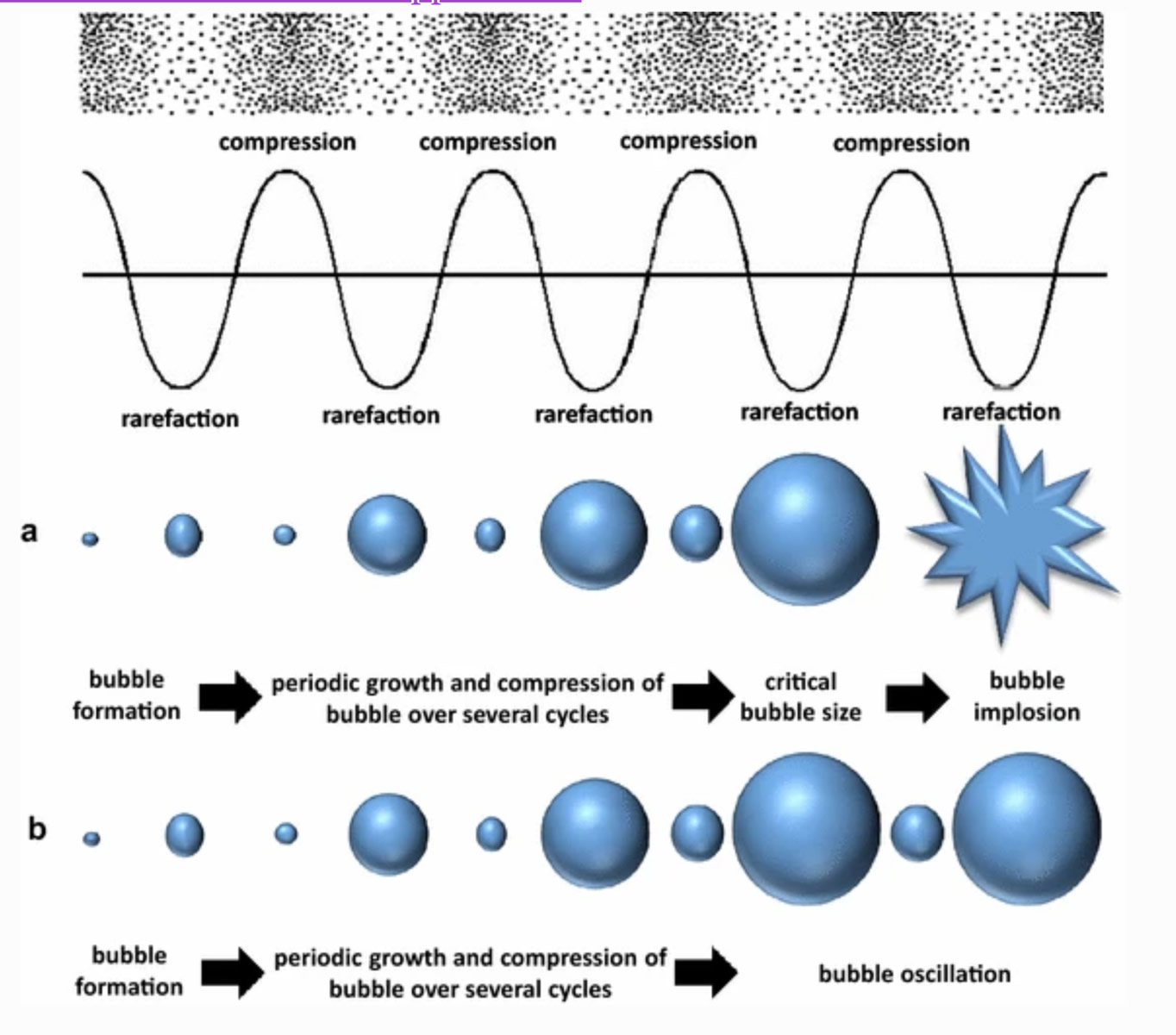
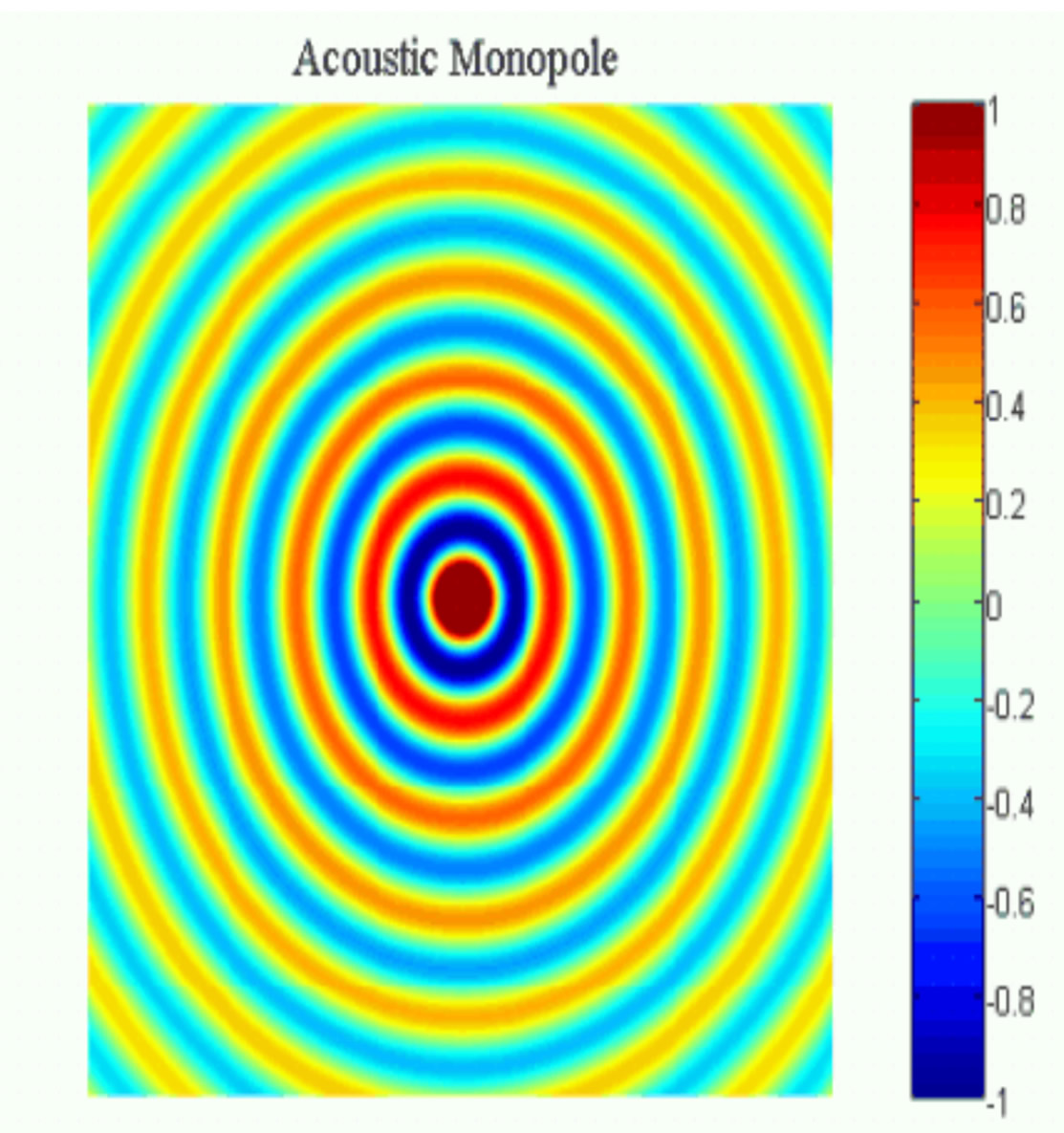
The expansion and contraction of the bubble can be considered as a monopole excitation source.
Both the oscillation and implosion of the microbubbles generate a pressure field in the fusion area.
Impedance measurements, Al-Al and Cu-Al
- Impedance measurements conducted away from the welding area
- Similar procedure used to assess impedance improvement due to sonication
- Evaluation performed for both Al-Al and Cu-Al materials
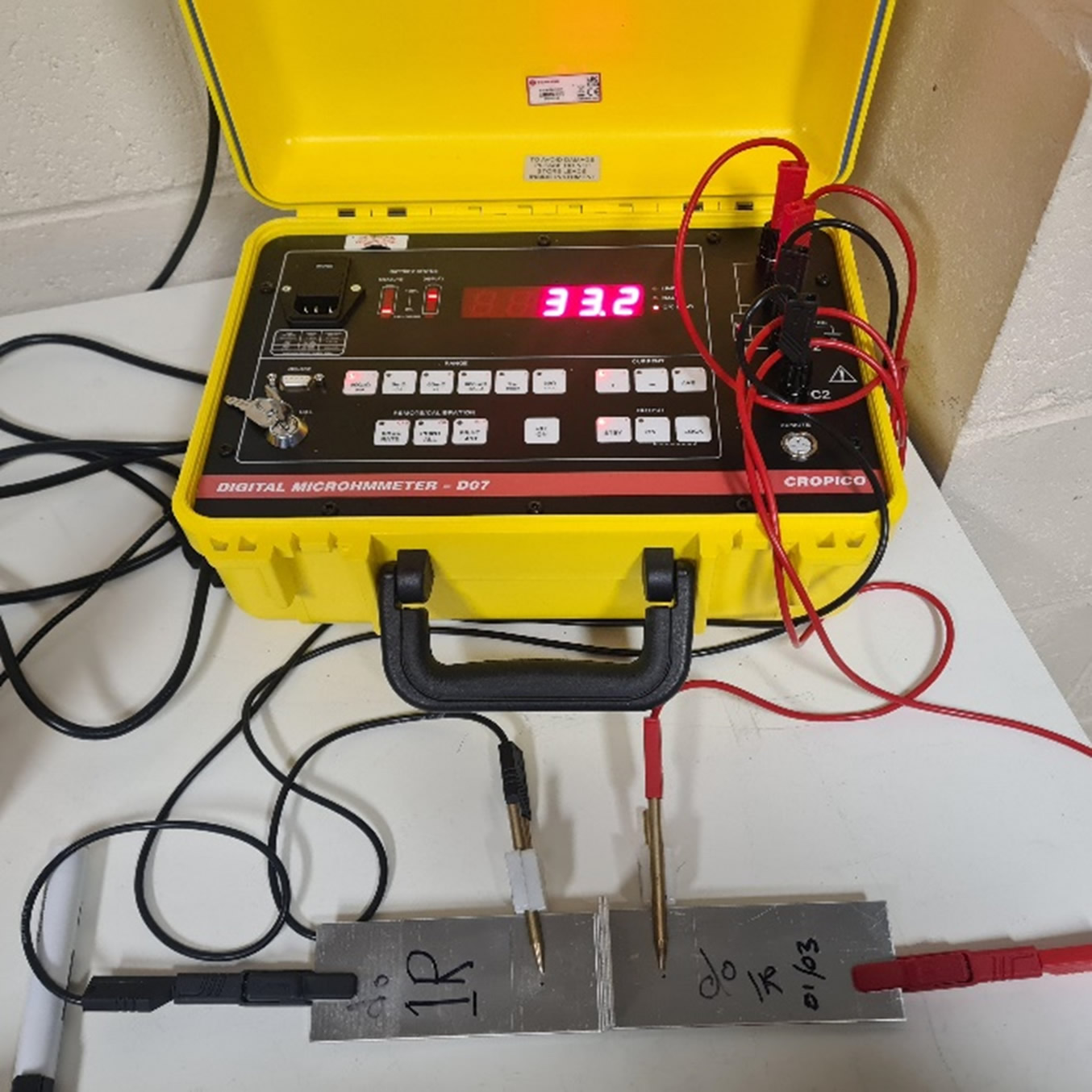
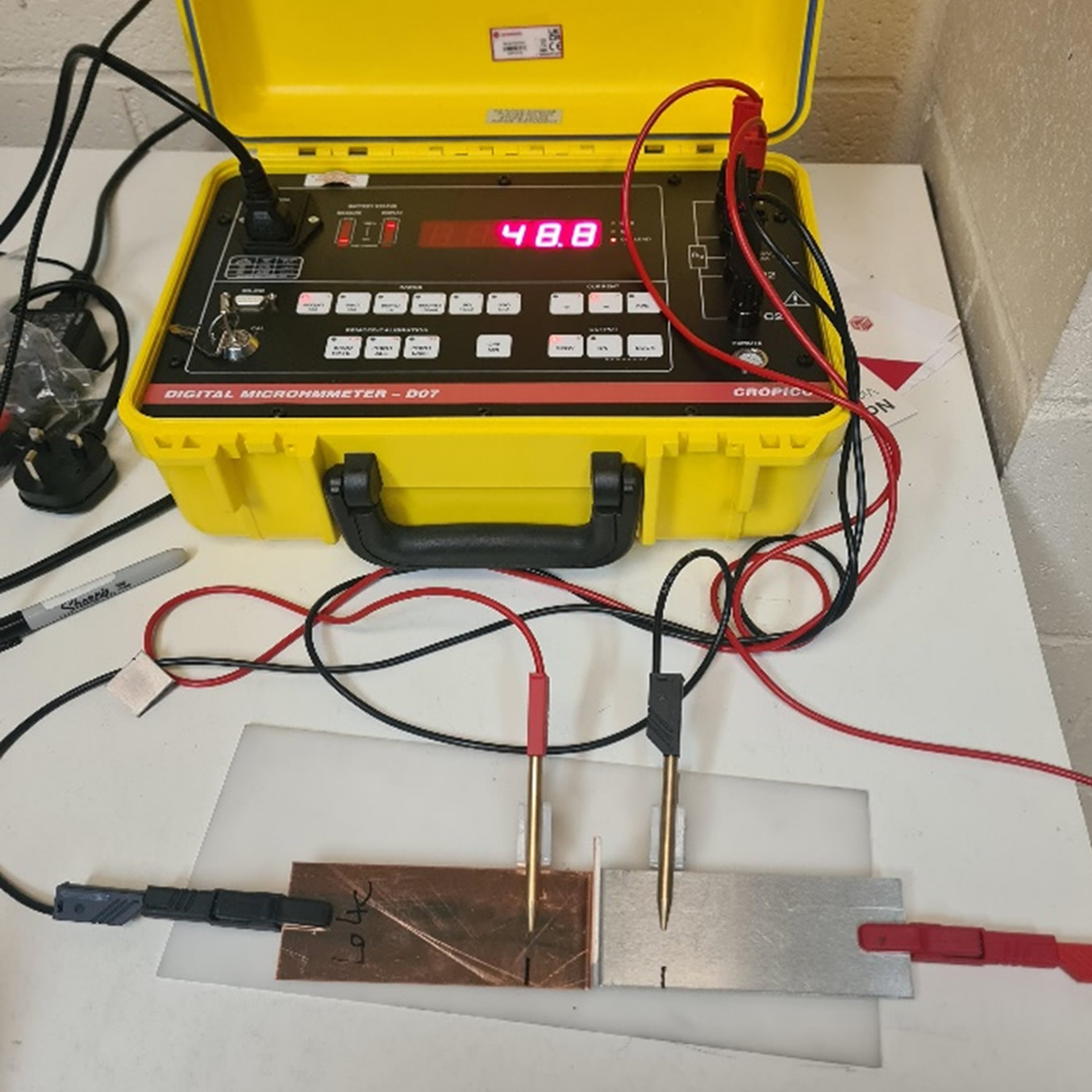
Experiments at Carrs and Brunel
Carrs Welding Technolgies Ltd
Aluminium – Aluminium
Welding trials were conducted using the L-shaped plates to replicate the welding done on cells. Using PUVT3, the ultrasound was applied in different configurations to further understand the impact of applying ultrasonic vibrations. The plates in this case were AL1050 to Al1050 and were pulled apart in a peel test method, allowing us to see the load vs extension. We then compared baseline (no ultrasound) results to welds with ultrasounds applied.
Copper to Aluminium
Similar Cu101-Al1050 trials were conducted alongside Al1050 trials to see the how ultrasound impacts the welding of dissimilar materials. Peel Tests were conducted on these welded plates to see how using PUVT3 impacts the weld. The welding of copper to Aluminium creates intermetallic compounds, making the welds very brittle. In previous trials using PUVT1, pull test results showed improvements to the strength and ductility, analysis on the PUVT3 trials were done to see if there is similar improvements. This would not only show that ultrasounds impact Cu/Al welds but also show that the PUVT3 method works.
Impedance Testing
An important factor to consider when welding cells is the impedance. Prior to conducting the pull test on the plates an impedance test was carried out. As with the pull test this will allow us to compare the results of a baseline weld to welds with ultrasound applied to it. The benefits of using this method is this method to test the quality of the weld is that its an non- destructive method of testing.
Brunel University
- Development of Contactless Ultra-sound device PUVT3. The directly mounted device used in UltraMAT has been developed further to be a contactless version, this allows easy applications of the battery welding connections, as there is no setup time for a short weld cycle application.
- Advanced testing of the welds, which are the battery connections to include Impedance testing and SEM analysis of the weld grain structure.
- Numerical modelling of the weld geometry and layout, to predict wave propagation of the PUVT through the structure and benefits.
- Numerical Simulation, to predict and explain the impedance change due to the welding.
Soni-Laser Project Reference: 10018077

Innovate UK is the UK’s innovation agency
Innovate UK is an executive non-departmental public body, sponsored by the Department for Business, Energy & Industrial Strategy.